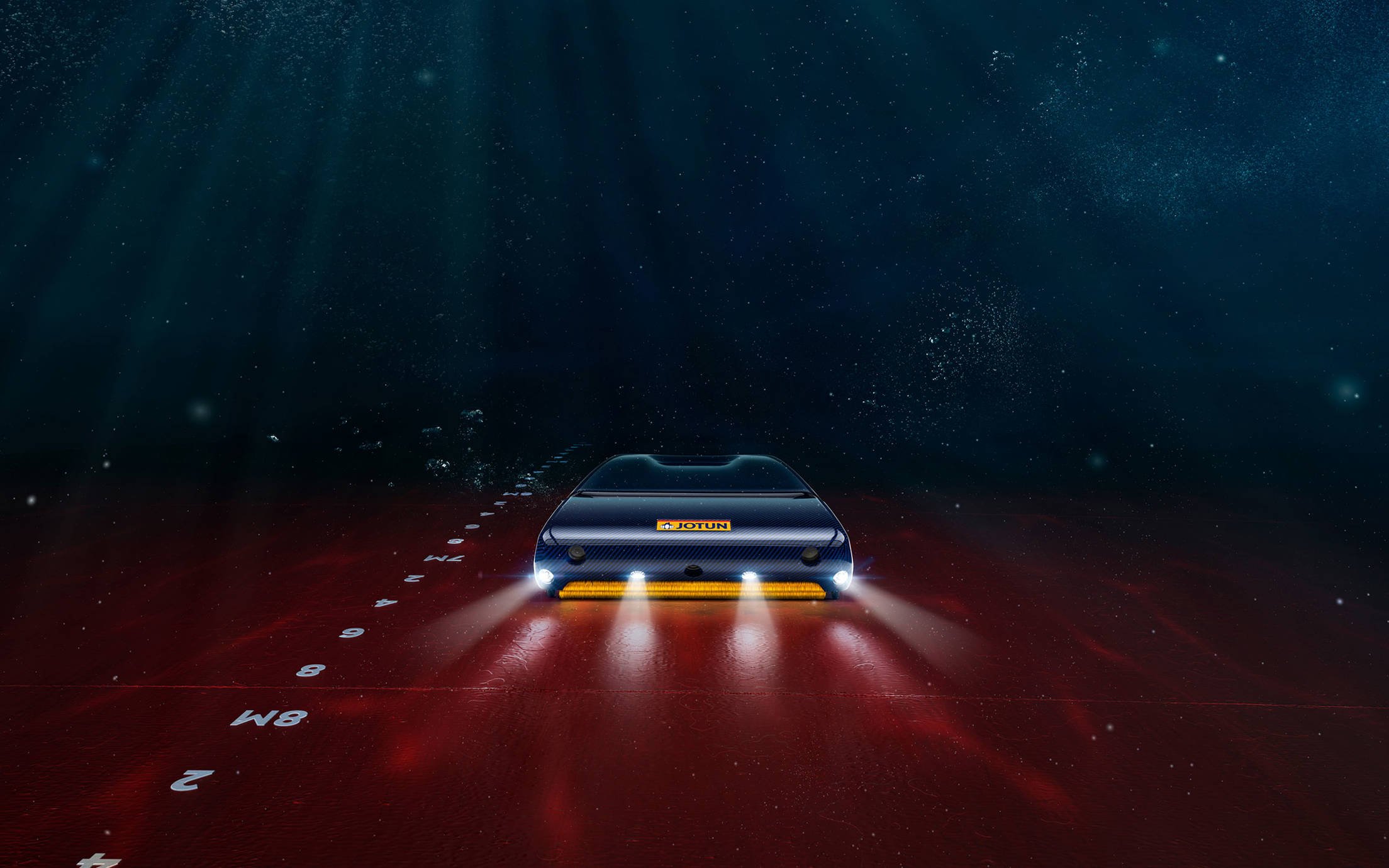
Hull Skating Solution
By combining robotics, big data and paint technology, this underwater robot can solve one of the oldest problems in shipping and help the shipping industry reduce its carbon footprint. Read on to discover how.
November 21, 2021
As a global, multinational manufacturer of paint and coating solutions — with factories, warehouses, and sales offices in 47 countries — there’s an inevitable environmental cost to Jotun’s operations.
Within today’s conversation of sustainability and environmental efforts, Jotun has taken a holistic and structured approach, finding innovative ways to improve its environmental performance, one step at a time.
So far, this approach has led to several changes and initiatives. The results are as diverse as they are positive.
According to Bjørn Skjelby, Group Technical Director HSEQ, a functional system for Health, Safety, Environment & Quality (HSEQ) Management is key to managing the environmental impact of a company.
“The system we’ve set up creates a structure of responsibilities in the organisation, with each Jotun site working towards universal goals,” he says.
“By establishing clear targets and key performance indicators (KPIs), and assigning individuals to manage specific environmental issues, we can track our progress and see where we need to put our resources.”
Standardised reports, verified by scheduled audits, provide the data needed to perform assessments, make recommendations, and help ensure each site is operating in compliance with company policy.
“What can be measured can be managed,” Skjelby states. “And because there is a clear link between improved environmental performance and efficiency, this means we can also reduce costs.”
While investments in new equipment may be appropriate in some cases, sound environmental results can also be achieved through efficiency improvements — as is the case with Jotun’s powder coatings factory in Nilai, Malaysia. Over a three-year period, the factory doubled its energy efficiency.
“By implementing best practices, maintenance routines and by focusing on root-cause analysis, we resolved product quality issues, avoided returns and spent considerably less energy,” says Operations Manager Tomas Drahovzal.
The company also installed 2236 solar panels in October 2021, generating up to 26 per cent of total electricity used in the Nilai factory. Return of investment is 3.5 years based on electricity savings and tax incentive from local authorities, adds Drahovzal.
In Qingdao, China, steps have been made to meet another government-sponsored initiative. Consistent with the Industrial Green Development Plan, Jotun’s factory has taken several actions.
“We implemented 12 individual projects”, says Operations Manager, Mark Xu.
“From installing hand-dryers to switching out storage solutions, our efforts managed to cut energy consumption as well as costs.”
With Jotun’s holistic approach, the measures are not limited to the factory itself. Raw materials and waste management is part of the bigger picture.
“We also did a lot of work on waste disposal, implementing systems for recycling aluminium cans, solvents and resins”, says Xu. “And by switching from 25kg bags to 500kg bags of raw materials, waste was reduced by 67 per cent.”
“Recycled Intermediate Bulk Container (IBC) has been taken to deliver finished goods in the marine business, which is environment friendly, reduces the hazardous waste in shipyards and is highly recognised by our customers.”
Located in a region especially sensitive to water waste, Jotun’s newly developed Oman facility has factored scarcity into the picture, taking every measure to use as little water as possible.
Manohar Neelakandan, Operations Manager, explains that “by switching to reprocessed water for landscaping, watering plants at dusk or dawn and choosing less water-intensive greenery, we not only save water, we lowered our water disposal costs by 60 per cent.”
With energy efficiency being a critical part of the green building certification, Jotun decided to design and build its new R&D centre in Sandefjord, Norway according to the Norwegian adaptation of BREEAM (Building Research Establishment Environmental Assessment Method). The result is a highly functional and effective building, with many smart and visual features. Still, one of the most energy-saving features of the new facility is invisible.
“Pumps draw cold seawater from the adjacent fjord, into a large tank”, explains HVAC Engineer Roar Elsebutangen. “Here, a process involving highly efficient heatpumps distributes heating and cooling to the entire building year around, also including walkways and parking structure in wintertime, keeping them free from snow and ice.”
With such a wide range of efforts all yielding results in Jotun’s environmental performance, it’s no wonder universal goals and guidelines make a difference. Group Technical Director HSEQ Bjørn Skjelby acknowledges that managing Jotun’s approach is complicated by the number of factories, warehouses and sales offices in the network. But he also sees strength in diversity and trusts local personnel to find the best solutions.
“Managers are empowered to find solutions that work within the structure of the guidelines,” says Skjelby. “In this way, each site serves as a laboratory of innovation, helping us to collect and share best practices.”
By combining robotics, big data and paint technology, this underwater robot can solve one of the oldest problems in shipping and help the shipping industry reduce its carbon footprint. Read on to discover how.
Real-life testing is vital to understand how paint and coatings perform in every imaginable weather and climate condition. This is the story of how field-testing from pole to pole, and everywhere in between, ensures products that protect property anywhere in the world.
Renowned architects, ambitious designs and unique requirements. When the World Expo is on the agenda, nothing is spared.
A video is being shown
An image is being displayed
A brochure is being displayed